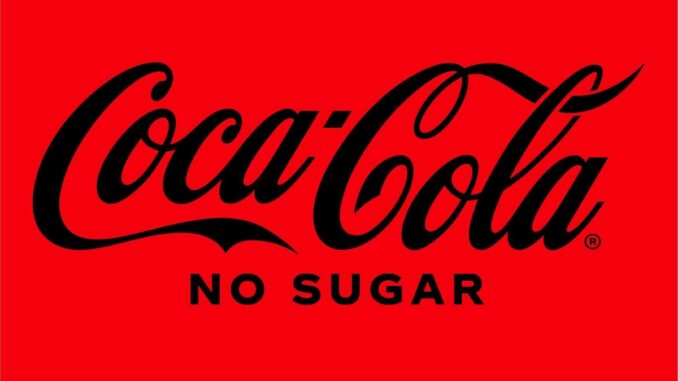
Unit Manager Processing
JOB DESCRIPTION
Coca-Cola Beverages Africa (CCBA) is the largest African Coca-Cola bottler, accounting for 40% of all Coca-Cola volumes on the continent. CCBA has an extensive footprint in Africa, employing over 17 000 employees, serving a combined population of over 300 million people across the continent.
The CCBA vision is to refresh Africa every day and make the continent a better place for all, growing successfully as a business and creating a better shared future for our people, customers, consumers, communities, planet and shareholders. We conduct ourselves with the utmost integrity for shared value and the greater good. We are a world class, customer-orientated, socially and environmentally conscious fast-moving consumer goods (FMCG) company that is driven by engaged, motivated and inspired employees.
Coca-Cola Beverages South Africa (CCBSA) has an exciting opportunity in our Manufacturing and Technical department. We are looking for a talented individual with relevant skills and experience for a Unit Manager: Processing role, which is based in Devland. The successful candidate will report directly to the Production Engineer in Devland, Gauteng.
KEY PURPOSE
To manage, lead and support the process support team in the achievement of cost effective and timeous supply of the correct quantity and quality of materials (syrup, treated water and steam) to relevant departments, in order to meet business and customer requirements.
Key Duties & Responsibilities
Processing Plant Management
- Plan for the unit to ensure that business strategy, goals, and objectives are met.
- Review production plans (daily and weekly), received from Supply Chain Planning to establish production targets for every shift on the unit.
- Maximise production throughput and conformance to quality and minimise waste of product, ingredients, and auxiliary materials.
- Drive predictable and reliable production processes and outputs.
- Monitor indicators that reflect the business strategy, key goals and objectives.
- Define and monitor KPI’s to ensure that Short Interval Control (SIC) is entrenched and all targets are achieved.
- Take appropriate corrective action to prevent deviations to target.
- Manage by walking about to ensure first-hand knowledge of operations.
- Communicate the latest/updated standards and requirements to eliminate standard-related causes of non-conformance.
- Partner with Quality Assurance (QA) to resolve problems related to sub-standard purchased ingredients to permanently eliminate root causes.
Drive Performance Improvement
- Structure and facilitate problem solving using suitable multi-disciplinary teams and appropriate techniques to eliminate root cause and close loops.
- Manage gaps using a formal process to track problems and their resolution.
- Identify and prioritise performance improvement opportunities using key KPI’s and appropriate analysis.
- Plan, implement and manage performance improvement projects.
Lead the Application of Asset Care (AC) Practices
- Review and manage all preventative maintenance tasks, including autonomous maintenance, for all equipment failures.
- Communicate equipment failures, trends and KPI’s for Autonomous Maintenance (ATM).
- Take into account opportunistic maintenance and cleaning of equipment when organizing production.
- Manage recording of equipment failures and tracking of trends to ensure they are prioritized and resolved.
- Review and manage all preventative maintenance tasks, including ATM, for all equipment failures
Manage Quality in the Processing Unit
- Measure and manage quality compliance by identifying and incorporating Quality at Source targets into the relevant team goals.
- Ensure that the team’s capability allows for effective and efficient quality management practices
- Ensure that equipment and instruments are kept calibrated, maintained and fit for use to preserve the integrity of analysis data.
- Monitor compliance to the quality assurance systems, procedures and standards and take corrective action to prevent recurrence where required.
- Ensure that audit review processes are done and aligned to global standards audit process.
Manage Health, Safety, Environment and Risk
- Manage employee awareness of and training in Health and Safety, which may include signage, issuing and maintenance of PPE.
- Manage compliance to safety procedures in accordance with legislative and business requirements, as well as documentation and clearance to work permits.
- Conduct investigations and submit reports of incidents and accidents in accordance with company and legislative requirements.
Manage Cost Plans and Costs
- Review expense and capital budgets quarterly so that planned expenses are managed effectively within budgetary parameters.
- Report on the budget expenses monthly.
- Identify variances and take corrective action to control costs, working with the Unit Manager: Utilities, Team Leaders and any other relevant employee.
- When required, identify, prepare and motivate project plans for approval as per the Operational Readiness meetings guidelines.
Manage Human Resources
- The effective management of allocated team, to allow for the achievement of set goals.
- Create an environment where the team is engaged and are achieving high-quality work output.
- Initiate, develop and maintain relationships according to collective agreements, conditions of employment, core values, disciplinary code and strategies.
- Ensure the continuous development of allocated team to allow for the effective and efficient functioning of the manufacturing unit.
- This includes driving the completion of CAP guide assessments for team.
- Ensure regular engagements with team to ensure alignment and the addressing of needs and risks as they may arise.
- Apply the PERFORM Way to own performance and that of team.
Skills, Experience & Education
- A minimum of a Matric and a 3-year relevant technical tertiary qualification (e.g. food technology; chemistry; chemical engineering
- A minimum of 3-5 years (Small Plant/Single Line) production and leadership experience in a FMCG environment.
- A minimum of 5+ years (Large Plant /Multiple Lines).
Competencies
Good Communication:
The ability to express oneself clearly in conversations and interactions with others and tailors the content of speech to the level and experience of the audience.
Problem Solving:
Use rigorous logic and methods to solve difficult problems with effective solutions; probes all fruitful sources for answers; can see hidden problems; is excellent at honest analysis; looks beyond the obvious and doesn’t stop at the first answers.
Planning:
The ability to apply planning skills in order to, schedule activities and prioritise resources in the achievement of an objective.
Customer orientation
Be dedicated to meeting the expectations and requirements of internal and external customers; gets first-hand customer information and uses it for improvements in products and services; acts with customers in mind; establishes and maintains effective relationships with customers and gains their trust and respect.
Conflict Management
Steps up to conflicts, seeing them as opportunities; reads situations quickly; good at focused listening; can hammer out tough agreements and settle disputes equitably; can find common ground and get cooperation with minimum noise.
Directing Others
Is good at establishing clear directions; sets stretching objectives; distributes the workload appropriately; lays out work in a well-planned and organized manner; maintains two-way dialogue with others on work and results; brings out the best in people; is a clear communicator.
Leave a Reply